智能革新多维优化:CNC仿真软件赋能精密加工新境界
19429202025-03-19手机软件9 浏览
在制造业高速发展的今天,一个争议性问题始终存在:为何投入巨额资金购买的高端数控机床,仍会出现刀具碰撞、加工误差甚至批量报废?传统加工模式中,工程师们往往需要反复试错,耗费数周时间调试程序,而智能化的CNC仿真技术正试图打破这一困局。据统计,全球因加工路径规划不合理导致的机床维修成本每年超过120亿美元。这场由虚拟仿真驱动的精密加工革命,是否真能开启多维优化的新境界?
一、碰撞与误差:传统加工的痛点能否彻底消除?
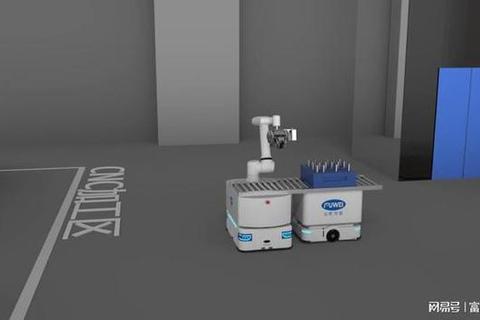
在浙江某汽车零部件企业的车间里,价值800万的五轴联动加工中心曾因刀具路径规划失误导致主轴损毁,直接损失达45万元。这正是CNC仿真软件要解决的核心问题——通过三维动态模拟,提前预判加工过程中的碰撞风险。例如触想智能为某国际客户定制的数控面板,借助DELMIA软件实现全流程仿真,使加工误差从±0.1mm降至±0.02mm。
智能革新多维优化:CNC仿真软件赋能精密加工新境界的核心突破在于物理引擎与算法融合。FANUC数控系统通过VERICUT软件构建的虚拟机床,可精确模拟主轴转速、进给量等200余项参数,某航空企业应用后刀具异常损耗率下降38%。这种将实际加工环境数字孪生化的技术,使得加工时间预估准确率提升至97%。
二、效率与成本:多维优化如何突破天花板?
东莞某模具厂曾面临复杂曲面加工效率低下的难题,传统编程需要3天完成的叶轮零件,应用PowerMill软件的自适应刀轨技术后,加工时间缩短至8小时。这得益于CNC仿真软件的三重优化维度:空间路径优化减少空走刀行程,时间维度通过切削参数仿真寻找效率峰值,成本维度则综合计算刀具寿命与能耗平衡点。
西门子NX软件的案例更具说服力。其基于遗传算法的智能排刀系统,在深圳某3C企业实现24把刀具的自动调度,使换刀频率降低42%,仅此一项每年节省耗材成本87万元。这种多维优化能力,让山东某重工企业的龙门铣床利用率从63%跃升至89%,真正实现了智能革新多维优化:CNC仿真软件赋能精密加工新境界的效能突破。
三、人机协同:智能决策如何重构制造生态?
在江苏某阀门制造基地,操作员王师傅的经历颇具代表性。过去需要20年经验积累的复杂零件编程,现在通过Hypermill软件的AI辅助模块,新手工程师也能在3小时内完成合格程序编制。这背后是机器学习算法对10万组历史加工数据的深度学习,可实现切削参数自动推荐、异常工况预警等智能决策。
更前沿的探索来自Tebis平台的数字孪生技术。其虚拟机床库包含全球1200种机床型号的精确模型,德国某精密仪器厂商通过云端协同仿真,实现中美德三地工程师对同一工件的实时协作编程,产品迭代周期压缩60%。这种打破地理边界的智能协同,标志着智能革新多维优化:CNC仿真软件赋能精密加工新境界正在重塑全球制造格局。
走向未来的行动指南
对于制造企业而言,把握三大关键点至关重要:首先优先选择具备物理引擎验证能力的软件(如VERICUT、Tebis),其次建立仿真数据与实际加工的反馈闭环,最后培养既懂工艺又擅仿真的复合型人才。某上市车企的实践值得借鉴:其通过Mastercam+PowerInspect组合搭建数字孪生体系,使新品首件合格率从72%提升至98%。在智能制造的赛道上,CNC仿真技术已不仅是工具,更是决定精密加工成败的战略性资产。